Steel deoxidation materials refers to the products that can help to remove the oxygen from molten steel. Deoxidation is a very important step in steelmaking. Oxygen will aggregate in the form of iron oxides, sulfur oxides, etc. during the solidification process of steel. These inclusions make the steel prone to cracking and cracking during processing and use. The increase in oxygen content will also reduce the ductility, impact toughness, and fatigue damage resistance of steel. The presence of oxygen in molten steel can cause pores and affect the mechanical properties and appearance quality of steel.
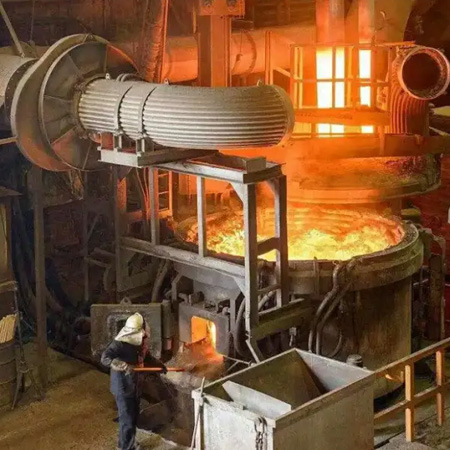
Using steel deoxidation materials can reduce the oxygen content in the steel and improve the properties of the steel, such as improving the purity of the steel and preventing aging; deoxidation process in steelmaking can also reduce the oxide content in the molten steel, thereby improving the purity of the steel, which is important for Improving the overall performance and quality of steel is critical.
According to the binding strength of various elements in molten steel to oxygen, the order from weakest to strongest is as follows: chromium, manganese, carbon, silicon, vanadium, titanium, boron, aluminum, zirconium, and calcium. Therefore, common steel deoxidation materials for steelmaking are iron alloys of which contains silicon, manganese, aluminum, and calcium.
Steel Deoxidation Products
Ferrosilicon is made from coke, steel scraps, quartz (or silica) as raw materials in an electric furnace. Ferrosilicon is a very regular deoxidizer in steelmaking. While deoxidizing, it can increase the temperature of molten steel and reduce the energy consumption of steelmaking.
Silicon-manganese alloy: Silicon-manganese alloy is a ferroalloy contain manganese, silicon, iron, etc. It is the most common alloying agent in steelmaking. Manganese can increase the strength of ferrite, improve the mechanical properties of steel, and enhance the strength, ductility, toughness and wear resistance of steel.
Aluminum: Pure aluminum has always been the main deoxidizer in the steelmaking industry and is suitable for the production of killed steel grades with high ductility and high impact toughness. The specific gravity of aluminum is much smaller than that of molten steel, so it easily floats on the surface of liquid steel and is easily to oxidize and burn, so the cost is higher.
Silicon Slag: Silicon slag is the bottom dross in smelting ferrosilicon and metallic silicon. It still contains a certain amount of silicon element inside. Silicon slag is a good steelmaking deoxidizer, which can effectively reduce steelmaking costs and improve manufacturer efficiency and product quality.
Silcon Carbon Alloy: The main components of silicon-carbon alloy include silicon (Si) and carbon (C). Its another name is high carbon silicon. It contains high silicon content and carbon content. It can replace traditional ferrosilicon, silicon carbide, Carburizer, etc., reduce the amount of deoxidizer.
Compound De-oxidation Material
Compound Deoxidation Material: Compound deoxidizer is generally a complex composed of several elements such as silicon, aluminum, calcium, manganese, and barium. For example, Silicon Aluminum Calcium Alloy, Silicon Aluminum Barium Calcium Alloy. Silicon Calcium Manganese Alloy.
The choice of deoxidizer depends on the degree of deoxidation required and the type of steel targeted. When using deoxidizers, it is necessary to consider the deoxidation efficiency, the morphology and distribution of deoxidation products, and the impact of deoxidation on other properties of steel. In addition, the price, availability and supply stability of steel deoxidation materials also need to be considered.