In the photovoltaic industry chain, silicon sludge is a by-product generated during the processes of silicon rod squaring and silicon ingot slicing. Silicon sludge is the raw material of regenerated silicon metal and silicon briquette. It is mainly classified into two types: crystalline silicon sludge and sliced silicon sludge. The total silicon content of crystalline silicon sludge ranges from 60% to 80%, with elemental silicon accounting for 35%-65%. In contrast, sliced silicon sludge has total silicon reaching 85%-97% and elemental silicon comprising 70%-95%. Since sliced silicon sludge constitutes 85%-90% of the total silicon sludge output, become the primary raw material for regenerated silicon. Taking China’s silicon wafer production of 227GW in 2021 as an example, the annual output of silicon sludge reached approximately 400,000 tons. Efficient recycling and utilization of this resource have become crucial for the sustainable development of the photovoltaic industry.
Fundamental Principles of Medium-Frequency Furnace Silicon Metal Production
Currently, medium-frequency induction furnaces are predominantly the equipment in China to smelt sliced silicon sludge. The core principle involves using electromagnetic induction heating to melt the silicon sludge and separating impurities through slag formation to ultimately produce silicon metal. The specific process includes:
Pretreatment of Silicon Sludge: The sludge must first be dried to remove moisture, thereby reducing energy loss and smoke generation.
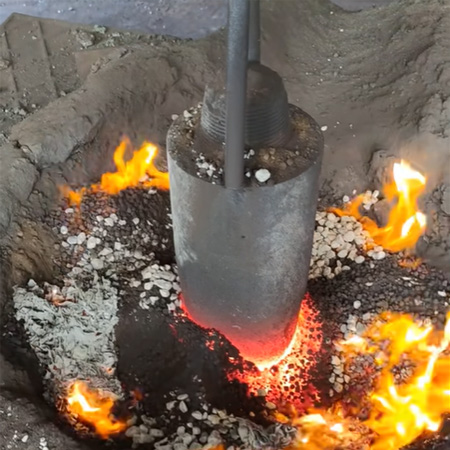
Smelting Process: The dried silicon sludge is fed into the medium-frequency furnace and melted at high temperatures of 1700-1750°C. Since the silicon dioxide (SiO₂) in the sludge has a melting point as high as 1713°C, quicklime (CaO) must be added as a fluxing agent to lower the slag’s melting point and improve its fluidity.
Silicon-Slag Separation: The density of molten silicon (approximately 2.33 g/cm³) is close to that of the slag (mainly composed of calcium silicate, with a density of about 2.5 g/cm³), making separation challenging. Effective separation requires precise temperature control and slag volume optimization.
Key Challenges and Optimization Measures in the Smelting Process of Silicon Sludge Regenerated Silicon
1 Challenges of the Silicon Sludge Control
Difficulty in Separation Due to Similar Densities: The close densities of molten silicon and slag lead to easy mixing, affecting the purity of the silicon metal.
Slag Fluidity Management: The high melting point of silicon dioxide necessitates the addition of lime to adjust slag composition (forming low-melting-point calcium silicate). However, excessive lime increases slag volume, exacerbating separation difficulties.
Temperature Control: The furnace temperature must be maintained above 1700°C to ensure complete slag melting. However, high temperatures accelerate the erosion of the furnace lining (typically made of ramming mix), leading to refractory material loss and increased slag volume.
2 Feeding and Operational Environment Issues
Hazards of Manual Feeding: The extremely fine particle size of silicon sludge poses risks during manual feeding. High temperatures (above 1600°C) cause residual moisture and organic matter to vaporize instantly, triggering explosions and smoke, which endanger workers’ health.
Labor-Intensive Slag Removal: After smelting, workers must manually remove slag at temperatures around 1700°C, resulting in harsh working conditions.
3 Process Optimization Directions
To improve silicon metal quality and smelting efficiency, the following aspects require focused control:
Raw Material Selection: Prioritize sliced silicon sludge with high silicon content (>90%) to minimize impurity introduction.
Precise Temperature Regulation: Use automated control systems to maintain stable molten pool temperatures and avoid localized overheating or slag solidification.
Fluxing Agent Ratio Optimization: Dynamically adjust lime addition to balance slag fluidity and volume.
Equipment Improvements: Adopt higher-refractory lining materials (e.g., silicon carbide bricks) to extend furnace lifespan.
Economic Benefits and Social Value of Silicon Sludge Regenerated Silicon
So far, the silicon sludge regenerated silicon metal models includes Silicon 553, 441, 3303, 2202 etc. There are also some off-standard models such as Silicon 853, 331, 221. Medium-frequency furnace smelting technology enables the resource utilization of photovoltaic waste. Also, it reduces the production cost of silicon metal. Based on 400,000 tons of silicon sludge, approximately 300,000 tons of silicon metal are recyclable. It will significantly decreasing reliance on primary silicon ore. In the future, the promotion of automated feeding systems, flue gas purification devices, and efficient slag treatment technologies will be hopefully to further enhance the environmental and economic performance of this process.
Silicon metal smelting from silicon sludge is a critical component of the green recycling system in the photovoltaic industry chain. Although the current process faces challenges such as high energy consumption and labor intensity, continuous technological improvements will ensure this method provides vital support for the sustainable development of the new energy industry.