Silicon raw materials mainly include silica, quartz sand, silicate ores, etc. Among them, silica is a natural ore with silicon dioxide (SiO2) as the main component. Quartz sand is also an ore containing high-purity silica. Quartz sand is the most commonly silicon raw material in silicon metal production. Its main composition is Si02 and usually contains a small amount of impurities. Currently, most silicon metal producers mainly extract silicon through smelting. Specifically, there are two methods: physical smelting and chemical smelting.
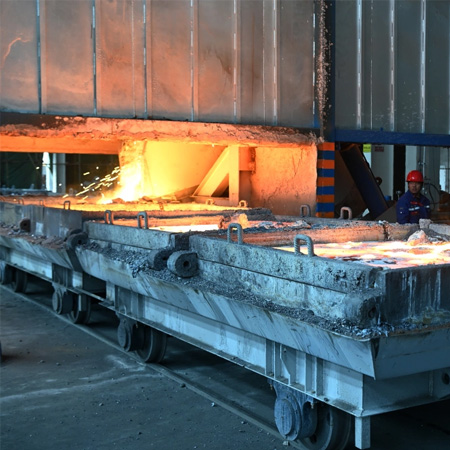
Physical refining of si metal
Physical refining mainly uses high-temperature treatment, using silicate ores and quartz sand to convert silica into silicon by reduction reactions. This method is usually apply in an electric furnace. The silicon raw material mixture go through the electric furnace for high-temperature heating. The heating time and temperature are strict to cause a reduction reaction between silicon dioxide and reducing agents. It generates silicon metal and carbon monoxide gas. Then through steps such as cooling, solidification and separation to get silicon metal. These silicon metals generally have a content of more than 98.5%. And also include off grade silicon metal 97 and other metallurgical grade silicon and chemical grade silicon metal models.
Chemical refining si metal production
Chemical smelting silicon metal production mainly uses wet methods. That is, dissolving silicon raw materials through chemical reactions and then reducing them to obtain silicon. This method is mainly carried out through alkali method and acid method.
The alkali method refers to reacting silicon raw materials with an alkaline solution to generate a silicate solution, and then reducing the silicate into silicon metal through heating and reduction. The solvent usually essential in the alkali method is sodium hydroxide solution. It reacts with the silicon raw material to generate sodium silicate, and then reduce the sodium silicate to silicon through the action of high temperature and reducing agent.
The acid method refers to reacting silicon raw materials with an acidic solution. It generates a hydrochloric acid solution containing silicon. Then it reducing the silicon in the hydrochloric acid solution through heating and reduction to obtain silicon products. The solvent usually used in the acid method is hydrochloric acid, which reacts with the silicon raw material to generate silicon chloride, and then reduces the silicon chloride to silicon.
Final Treatment
Generally speaking, the factory will break silicon metal into standard silicon metal lumps for easy use in the next step. For example, in the process of preparing silicon materials in the photovoltaic industry, silicon metal first needs to be liquid and cast into shape. Then, after the silicon metal is melted at high temperature, it can be cast into high purity silicon metal with the required shape. And then processed through cutting, polishing and other processing techniques to prepare the required silicon materials, such as silicon wafers, silicon rods, etc.
In short, the basic chemical principle of industrial production of silicon is to extract silicon raw materials to obtain silicon metal, then purify the silicon metal through refining, and finally prepare silicon materials. This involves two methods of physical smelting and chemical smelting, as well as multiple process steps such as dissolution, reduction, cooling, solidification, separation, casting, and processing.