Silicon metal plays a variety of roles in aluminum alloys, including cast and deformed aluminum. Silicon metal for aluminum alloy includes several regular Si metal models. Such as silicon metal 553, silicon metal 441. Silicon can form a compound called AlSi. Al-Si compounds can increase the strength of aluminum alloys, hardness and thermal stability. In addition, the addition of silicon can also increase the flow performance of liquid aluminum, making it easier to form complex-shaped products.
In cast aluminum alloys, the functions of silicon include: improving the high-temperature rheological properties of the alloy, reducing shrinkage and reducing the tendency of hot cracking. For AlSi alloys, the mass fraction of silicon is usually between 6.5% and 7.5%. When the mass fraction of silicon reaches 7.5%, the fluidity can be better.
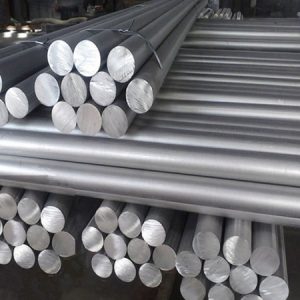
Application of Si Element in Al-Alloy
Adding silicon metal for aluminum alloy can also improve the electrical conductivity and heat dissipation of aluminum alloys, which makes silicon widely used in aluminum alloys to manufacture conductors and heat sink materials. When manufacturing cast aluminum products, the most commonly used AlSi aluminum alloy is 6 series aluminum alloy. For example, 6061 aluminum alloy plate is a common aluminum alloy. In addition, 5052, 6063, 7075, etc. are also common aluminum alloy models. The main additives of these aluminum alloys are Silicon Metal and Magnesium Ingot.
The content of silicon in aluminum alloys depends on the required aluminum alloy properties and application scenarios. Generally speaking, the silicon content in aluminum alloys should be in a certain range to achieve optimal performance and application effects. In the casting of aluminum alloys, the silicon content is usually between 0.2% and 2.5%.
The higher the silicon content, the higher the strength and thermal stability of the aluminum alloy. But it will increase the thermal expansion coefficient of the aluminum alloy. Therefore, during the casting process of aluminum alloys, the amount of silicon added should be adjusted according to the specific application scenario. The content of silicon in wrought aluminum alloys is usually low, usually less than 1.0%.
In summary, the addition of silicon should be in accordance with the specific aluminum alloy type and application scenario. In the process of aluminum alloys, the content of silicon should be set by experiments and simulations, based on the required properties.