Casting is the earliest metal thermal processing technology mastered by humans, with a history of about 6,000 years. Among the existing metal forming methods, the casting process is also a relatively economical one. Especially for forming parts with complex shapes or that are difficult to machine. For automobile wheel hub materials, aluminum alloy is more important in production. Magnesium alloy which made from magnesium Ingot and other metals, has the advantages of low density (about 2/3 of aluminum alloy), high specific strength and specific stiffness. Mg Alloy Magnesium Ingot also have good casting and cutting performance, high thermal stability, damping and noise reduction, etc. It is also a additive of wheel hub material.
The casting processes currently for magnesium alloy include gravity casting, pressure casting, squeeze casting and low pressure casting. Among them, low-pressure casting is one of the main forming methods of magnesium alloys. Its smooth filling and sequential solidification characteristics helps to produce high-quality magnesium alloy castings. However, the low-pressure casting process of magnesium alloy automobile wheels still needs to be further studied and improved. With the development of computer technology, numerical simulation technology is widely used. It’s mainly used in the development and optimization of casting processes. By simulating the casting process of castings, defects such as pores, shrinkage porosity, shrinkage cavities. And, Mg Alloy Magnesium Ingot can effectively predict the slag inclusions in castings. thereby shortening the product process development cycle and reducing production costs.
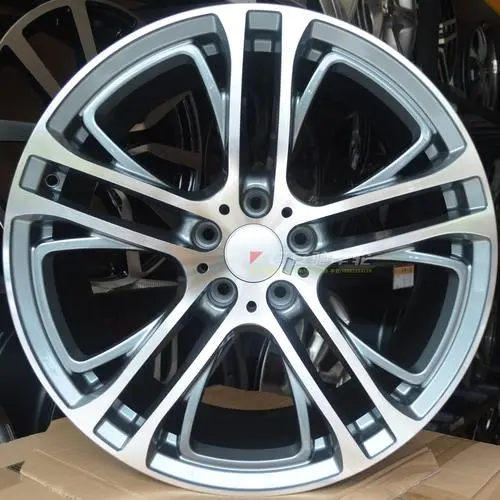
Magnesium alloy automobile wheel hub casting processes mainly include gravity casting, pressure casting, squeeze casting, low pressure casting and other methods. At present, aluminum and magnesium metal are important in industrial production. It’s because of their excellent castability, corrosion resistance and high specific strength. In order to solve the problems of large-size low-pressure cast A356 aluminum alloy wheel rim shrinkage, air leakage, and failure of the 90° impact test, We achieved sequential solidification by improving the rim cavity structure, and improved the efficiency by adding a cooling air box to the side mold. Just to improve the mechanical properties of the rim.
Under the general trend of automobile lightweighting and energy conservation and emission reduction, modern materials require more lightweight and high-strength properties. Compared with aluminum alloys, magnesium alloys are lighter, which is more conducive to weight reduction of cars and improved acceleration performance of cars. Experiments show that replacing the aluminum alloy wheels of new energy vehicles. Those vehicles with magnesium alloy wheels of the same size will increase its endurance by more than 8%. Based on these characteristics, magnesium alloy materials highlight their advantages in the industrial field. The low-pressure casting process of magnesium alloys has also been studied by many scholars. Therefore, the market will gradually increase the demand for Magnesium Ingot, especially for Mg Ingot 99.9, 99.95 and other models.