Magnesium alloys is an alloy based on magnesium ingot with other elements added. They are applicable in many industrial fields due to their light weight, high strength, good machinability, corrosion resistance, shock absorption and dimensional stability.
Its density is about 1.8g/cm3, so with the same strength, parts made of magnesium alloy will be lighter. In addition, magnesium alloy has low cutting resistance, which greatly improves processing efficiency and tool life. In terms of corrosion resistance, magnesium alloy has good corrosion resistance in air.
Common magnesium alloys components
The components of mg-alloy include magnesium, aluminum, zinc, manganese, titanium and other elements.
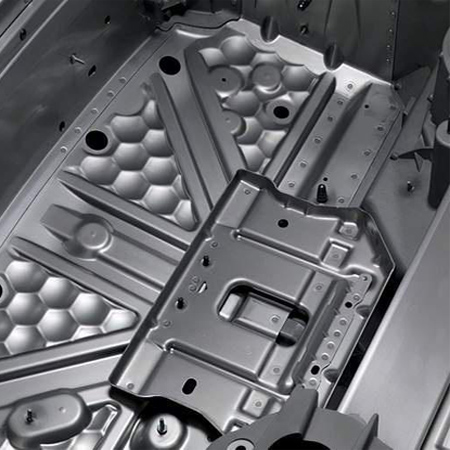
Magnesium is the basic element of magnesium alloys and has excellent properties . Such as light weight, high strength, and good thermal conductivity. As a rare metal, its acquisition cost is high, so Mg Alloy are more expensive.
Aluminum has a high content in mg alloys and is a commonly alloying element. By adding an appropriate amount of aluminum, the hardness and corrosion resistance will be better while reducing their ignition point.
Silicon has the effect of improving casting properties, improving thermal stability, and increasing strength and hardness. However, excessive silicon metal content will affect the plasticity, hot crack risk and toughness of mg alloys. So, silicon needs to be added within an appropriate range.
Zinc can improve the strength and corrosion resistance of mg alloys, while also improving its thermal stability and better durability, especially at high temperatures.
The content of manganese in magnesium alloys generally does not exceed 0.5%. It mainly plays the role of organic reduction, can improve the hardness and processing performance of magnesium alloys, and can also reduce its corrosiveness.
In addition, magnesium alloys often contain elements such as copper, sodium, and zirconium.
Magnesium Alloys Models
Common magnesium alloys models include AZ series (such as AZ31, AZ61, AZ91, etc.), AM series (such as AM50, AM60, etc.), ZK series (such as ZK10, ZK30, etc.), etc.
Among them, the AZ series magnesium alloy is the most common and is made of magnesium mixed with aluminum and zinc. AZ31 contains 3% aluminum and 1% zinc. AZ61 contains 6% aluminum and 1% zinc. AZ91 contains 9% aluminum and 1% zinc. The AM series mainly contains aluminum, manganese and other elements, while the ZK series contains zinc, manganese, zirconium and other elements.
Proper ingredient ratio can enable magnesium alloys to have optimized properties. For example, strength, hardness, toughness, refining resistance, corrosion resistance, lightweight, etc. Therefore, it is necessary to select a suitable magnesium alloy and adjust and improve the alloy composition according to actual needs.