Magnesium alloys often use magnesium as the basic element and also contain multiple elements such as aluminum, zinc, silicon, manganese, and copper. The functions of each elements in magnesium alloys varies. By adjusting the content and proportion of different Elements, we can get different applications of Magnesium alloys.
Aluminum Elements in Mg Alloys
Al: Improves mechanical strength, corrosion resistance, castability, fluidity, ductility and toughness and gradually decreases as the aluminum content increases. Aluminum is one of common alloying elements in magnesium alloys. Aluminum and magnesium can form a finite solid solution, with a saturated solubility of 12.7% at the eutectic temperature. While improving the strength and hardness of the alloy, it can also broaden the solidification zone and improve casting performance. Since solubility decreases significantly with temperature, magnesium-aluminum alloys can be heat treated. When the aluminum content is too high, the stress corrosion tendency of the alloy increases and the brittleness increases. Aluminum-Magnesium alloy is one of the most common magnesium alloy models.
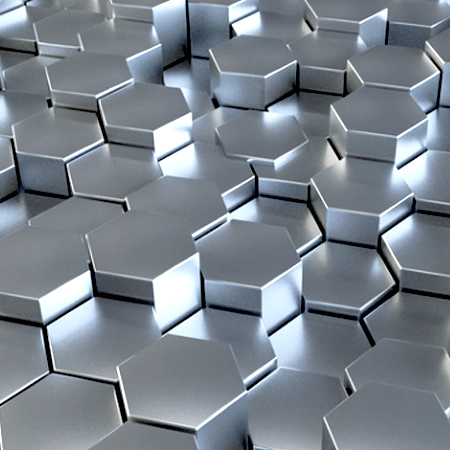
Zinc in Magnesium Alloys
Zn: Improves mechanical strength and corrosion resistance, and can improve the fluidity and mechanical properties of magnesium alloys. However, when the content exceeds 1%, it will cause high-temperature thermal brittleness of the alloy. The maximum solid solubility of zinc in magnesium is 6.2%. It is another very effective alloying element besides aluminum and has the dual functions of solid solution strengthening and age strengthening. Zinc is often combined with aluminum to increase room temperature strength. Zinc is also combined with zirconium, rare earths or thorium to form precipitation-strengthened magnesium alloys with higher strength. Due to the large interval between crystallization temperatures of high-zinc-magnesium alloys, the fluidity of the alloy is greatly reduced, resulting in poor castability. In addition, zinc can also reduce corrosion caused by the presence of iron and nickel.
Metal Silicon Applications in Magnesium Alloys
Silicon – Si: Silicon is a common additive in magnesium alloys. It mainly plays the role of increasing the strength, stiffness and heat resistance of magnesium alloy materials. At the same time, it can improve the corrosion resistance of magnesium alloy and prevent oxidation and corrosion on the surface of magnesium alloy. The addition of silicon can improve the mechanical properties of the alloy such as tensile strength, stiffness and hardness. At the same time, silicon can improve the thermal stability and thermal softening temperature of magnesium alloys, and reduce the creep deformation of the alloy at high temperatures. The addition of silicon can also improve the corrosion resistance of the alloy, especially in corrosive environments at high temperatures. In magnesium alloys, silicon metal is generally added to increase the silicon content.
Copper and Nickel Elements in Magnesium Alloys
Copper and Nickel – Cu:Ni: Copper and nickel drastically increase the oxidation tendency of the alloy in the molten state and simultaneously reduce the corrosion resistance of the alloy. They are harmful impurities in magnesium alloys. Copper is an element that affects the corrosion resistance of magnesium alloys. When the addition amount is not less than 0.05%, the corrosion resistance of magnesium alloy will be significantly reduced. But it can improve the high temperature strength of the alloy.
Iron and Other Elements in Magnesium Alloys
Iron – Fe: Reduces the mechanical properties and corrosion resistance of the alloy. Like copper, iron is also an element that affects the corrosion resistance of magnesium alloys. Even minute amounts of impurities can significantly reduce the corrosion resistance of magnesium alloys. Usually the average iron content in magnesium alloys is 0.01%-0.03%. To ensure the corrosion resistance of magnesium alloys, the iron content must not exceed 0.005%https://highrisemetal.com/product/silicon-metal/
Beryllium-Be: Reduces the oxidation rate of magnesium alloy in the molten state. Trace amounts of beryllium can effectively reduce the oxidation of the metal melt surface during the melting, casting and welding processes of magnesium alloys. At present, both die-cast and forged magnesium alloys have successfully applied this property. When the beryllium content is too high, there will be a grain coarsening effect, so sand-cast magnesium alloys need to be used with caution, and the content of deformed magnesium alloys must also be controlled.
Manganese – Mn: can greatly improve corrosion resistance and control the iron content in the alloy.
Rare earth element –RE: Improves high temperature creep properties.