Ferro Silicon and Silcon Carbide both are important materials in metallurgy industry. But, different applications FeSi SiC are in many aspects. First of all, ferrosilicon is an alloy of silicon and iron, which have various grades of Ferrosilicon 65%, FeSi72, Ferrosilicon 75, according to the silicon content.
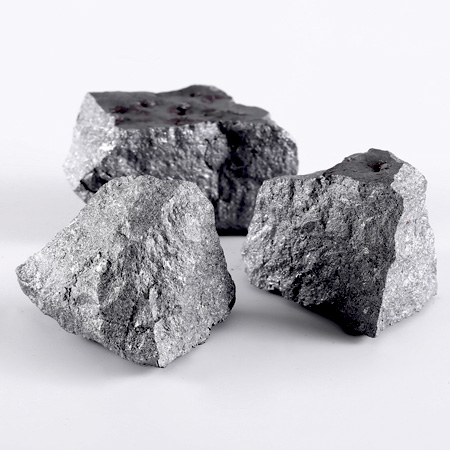
Applications of Ferro Silicon
(1) Used as deoxidizer and alloying agent in the steelmaking industry. The chemical affinity between silicon and oxygen is very large, so ferro silicon is a strong deoxidizer for steelmaking and in precipitation and Diffusion deoxygenation. Adding a certain amount of silicon to steel can significantly improve the strength, hardness and elasticity of the steel. Therefore, it is useful in smelting structural steel (containing 0.40-1.75% silicon), tool steel (containing SiO.30-1.8%), Ferrosilicon is also an alloying agent in steel (containing Si 0.40-2.8%) and silicon steel for transformers (containing 2.81-4.8% silicon).
(2) Used as inoculant and spheroidizing agent in the cast iron industry. Cast iron is an important metal material in modern industry. It is cheaper than steel, easy to melt and smelt, has excellent casting properties and much better vibration resistance than steel. Especially ductile iron, its mechanical properties are equal to or close to those of steel. Mechanical behavior. Different Applications FeSi SiC. Therefore, in the production of ductile iron, ferro silicon is an important inoculant (helping to precipitate graphite) and spheroidizing agent. .
(3) Used as reducing agent in ferroalloy production. Not only is the chemical affinity between silicon and oxygen very high, but the carbon content of high-silicon ferrosilicon is very low. Therefore, high-silicon ferrosilicon (or silicon alloy) is a commonly used reducing agent in the ferroalloy industry when producing low-carbon ferroalloys.
(4) Use in other aspects. Ground or atomized ferrosilicon powder can be used as a suspended phase in the mineral processing industry.
Silicon carbide is a synthetic raw material, using natural silica (silica sand) and coke (or anthracite) with a Si02 content of not less than 97% as the basic raw materials, adding a small amount of salt and sawdust, and using a resistance furnace at a temperature of 2000-2500~C synthesis. It also has many uses:
Applications of Silicon Carbide
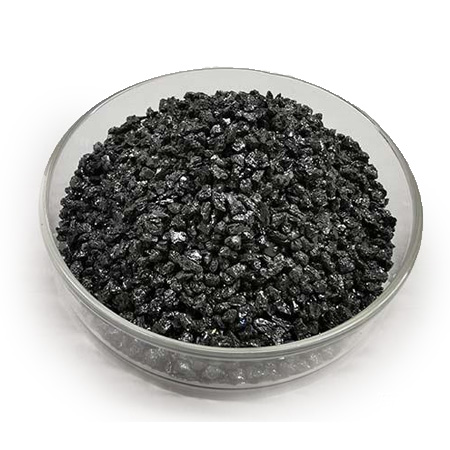
(1) The application in the non-ferrous metal smelting industry is to use silicon carbide with high temperature resistance, high strength, good thermal conductivity, and impact resistance as high-temperature indirect heating materials, such as pot distillation furnaces. Distillation furnace trays, aluminum electrolytic cells, copper melting furnace linings, arc plates for zinc powder furnaces, thermocouple protection tubes, etc. Different Applications FeSi SiC in many fields.
(2) Applications in the steel industry utilize the corrosion resistance of silicon carbide. Resistant to thermal shock and wear. It has good thermal conductivity and can be used for lining large blast furnaces to extend its service life.
SiC Application in Steel
(3) Application in the metallurgical mineral processing industry. Since the hardness of silicon carbide is second only to diamond, it has strong wear resistance and is an ideal material for wear-resistant pipes, impellers, pump chambers, cyclones, and linings of ore hoppers. Its wear resistance The performance is 5-20 times that of cast iron and rubber. It is also one of the ideal materials for aviation runways.
(4) Building materials ceramics and grinding wheel industrial applications utilize their thermal conductivity. Thermal radiation, high thermal intensity and the characteristics of manufacturing thin plate kiln furniture can not only reduce the capacity of the kiln furniture, but also improve the filling capacity of the kiln and product quality, shorten the production cycle, and are ideal indirect materials for baking and sintering of ceramic glazes.