Deoxidation process in steelmaking is very important. Oxygen is inevitable in molten steel. In oxygen-lancing process, the oxygen content will continue to increase due to the oxidation of the molten steel and the impurities. When it solidifies, it will react with the molten steel to form crystals. At the same time, ferrous oxide will also be generated. Due to the oxidation in the molten steel, The presence of ferrous iron will destroy the cast billet, thereby affecting the quality of steel products. What’s more, it will cause deformation problems, hot brittleness, and oxidation problems of steel.
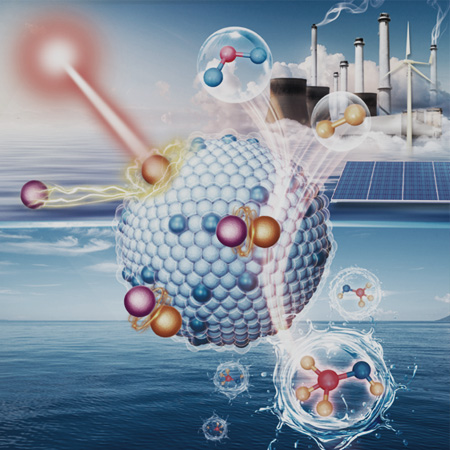
Therefore, the de-oxidation is an integral part of the steelmaking process. Deoxidizers like Ferro Silicon, Ferromanganese, Compound De-Oxidation Materials help to improve the performance, stability and purity of the steel, thereby ensuring the quality and reliability of the final product.
Deoxidation of steelmaking is a complex process involving multiple steps and reactions. In the steelmaking process, impurities in pig iron such as carbon, silicon, manganese, phosphorus, etc. need to be oxidized in the beginning. This is the reaction process during the oxidation period. Subsequently, desulfurization and deoxygenation reactions process will occur during the reduction period. The purpose of deoxidation is to remove oxygen from molten steel, because the presence of oxygen in molten steel will have adverse effects on the quality of steel.
Deoxidation Materials for Steelmaking
The deoxidation process in steelmaking is mainly proceeds with adding deoxidizers. Common deoxidizers include ferrosilicon 75, HC/MC ferro manganese, aluminum, etc. These deoxidants can react with FeO in molten steel to generate oxides, which are then discharged through the slag or absorbed by the molten steel to achieve deoxidation. For example, silicon has a strong affinity with oxygen. After adding ferrosilicon, the following deoxidation reaction can occur:
[2FeO + Si = 2Fe + SiO]
The generated silica is lighter than the molten steel. It will float on the surface of the molten steel thereby removing the oxygen in the steel. By this it can significantly improving the strength, hardness and elasticity of the steel. Meanwehile increase the magnetic permeability of the steel, and reduce the hysteresis of the transformer steel. loss.
In addition to the use of deoxidizers, there are other deoxidation methods, such as diffusion deoxidation and precipitation deoxidation. Diffusion deoxidation is to reduce the oxygen content of molten steel by spreading powdery deoxidizer on the slag surface and utilizing the diffusion behavior of oxygen to transfer it into the slag. Precipitation deoxidation is to add block deoxidizer (such as ferrosilicon block) directly into the molten steel, and the deoxidizer reacts with FeO to cause deoxidation.
Common dexodizer models includes ferrosilicon, ferrosilicon 72. High Carbon and Medium Carbon Ferro Manganese. Sometimes, in order to save cost, many steelmills also chose to use Silicon Slag or other compound deoxidizers. Those products contains certain composition of silicon or other oxyphilic element like Aluminum, Calcium, etc. So those models can also have good performance in de-oxidation.
In general, the deoxidation process is a key step to ensure the quality of steel. It not only removes non-metallic inclusions, but also removes oxygen from the steel to obtain high-quality steel products.