In the realm of aluminum alloys, certain elements play crucial roles in enhancing their properties. Copper, manganese, and zinc are among these vital elements. Copper Zinc Manganese Elements in Aluminum Alloy each are contributing to the strength, durability, and overall performance of aluminum alloys. Let’s explore how these elements function and interact within aluminum alloys.
Copper Element in Aluminum Alloys
Copper is a significant alloying element in aluminum alloys, known for its solid solution strengthening effect. Additionally, the CuAl2 compound precipitated during the aging process provides a pronounced aging strengthening effect. The copper content in aluminum alloys typically ranges from 2.5% to 5%. However, the optimal strengthening effect is when the copper content is between 4% and 6.8%. Consequently, most high-strength aluminum alloys contain copper within this range. Besides copper, aluminum-copper alloys may also include small amounts of silicon metal, magnesium metal, manganese, chromium, zinc, and iron to further enhance their properties.
Zinc Element in Aluminum Alloys
Zn is also an important aluminum alloy element, which can significantly improve the strength, corrosion resistance and processability of aluminum alloys. Zinc ingots are the most common metal zinc product. When zinc exists alone in aluminum, its improvement in the strength of aluminum alloys under deformation conditions is very limited. Moreover, the zinc element will also bring about the tendency of stress corrosion cracking of aluminum alloys. However, when zinc ingot and magnesium ingot adding into the aluminum liquid at the same time, the two form a strengthening phase MgZn2, which significantly strengthens the alloy. When the MgZn2 content increase from 0.5% to 12%, the tensile strength and yield strength will significantly increase. When the magnesium content exceeds the amount required to form the MgZn2 phase, supplementary strengthening will also occur.
By adjusting the ratio of zinc to magnesium, the tensile strength can be improved, and stress corrosion cracking resistance can be enhanced. In super-hard aluminum alloys, the optimal zinc-to-magnesium ratio is typically around 2.7, which maximizes stress corrosion cracking resistance. Adding copper to an Al-Zn-Mg alloy to form an Al-Zn-Mg-Cu alloy results in the strongest aluminum alloys, making them essential in the aerospace, aviation, and power industries.
Manganese Element in Aluminum Alloys
At the eutectic temperature of 658°C, manganese’s maximum solubility in the α solid solution is 1.82%. The strength of aluminum alloys increases with the solubility of manganese. The elongation reaches its peak when the manganese content is around 0.8%. Unlike some other alloys, Al-Mn alloys are non-age hardening, meaning they cannot be strengthened through heat treatment. Manganese helps prevent recrystallization in aluminum alloys, raises the recrystallization temperature, and significantly refines the recrystallized grains. This refinement occurs because the dispersed MnAl compounds hinder the growth of recrystallized grains. Additionally, MnAl compounds can dissolve impurity iron, forming (Fe, Mn)Al6 and mitigating the harmful effects of iron.
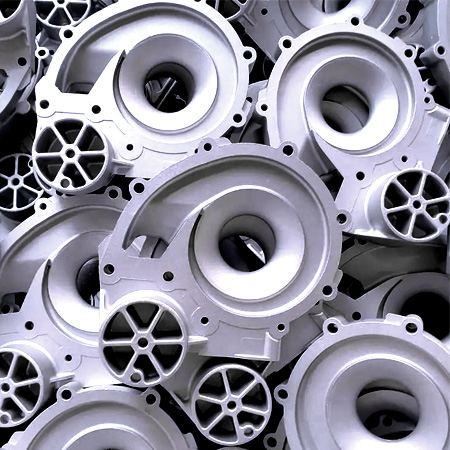
Manganese is common additive alongside other elements alloying agent such as silicon metal, magnesium metal, and others to form multi-element aluminum alloys. Consequently, manganese is a common component in most aluminum alloys.
While adding Copper Zinc Manganese Elements in Aluminum Alloy, incorporating aluminum titanium boron master alloy can further refine the grains of aluminum alloys, enhancing the effects of copper, manganese, and zinc. This master alloy helps achieve better grain refinement, ensuring the aluminum alloys perform optimally in their respective applications.
In summary, just like the role of silicon and magnesium in aluminum alloys, Copper Zinc Manganese elements in Aluminum alloy are integral to the development of high-performance aluminum alloys. Their specific roles and interactions define the properties of these alloys, making them suitable for a wide range of applications from automotive to aerospace and beyond. Understanding and optimizing the use of these elements continue to be crucial in advancing aluminum alloy technology.